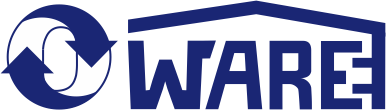
Send us an enquiry to obtain additional information about our Warehouse Management System. We will analyze your enquiry and return to you shortly by email or phone.
SALIENT FEATURES
- Complete internal supply chain from Gate-In to Gate-Out
- Fully integrated with SAP ERP for inbound and outbound transactions
- On-premise and Cloud option
- Multiple warehouses on a single instance
- Warehouse and non-Warehouse locations
- Manual and ASRS operations
- Real-time integration with WCS systems
- Android app for handheld terminals
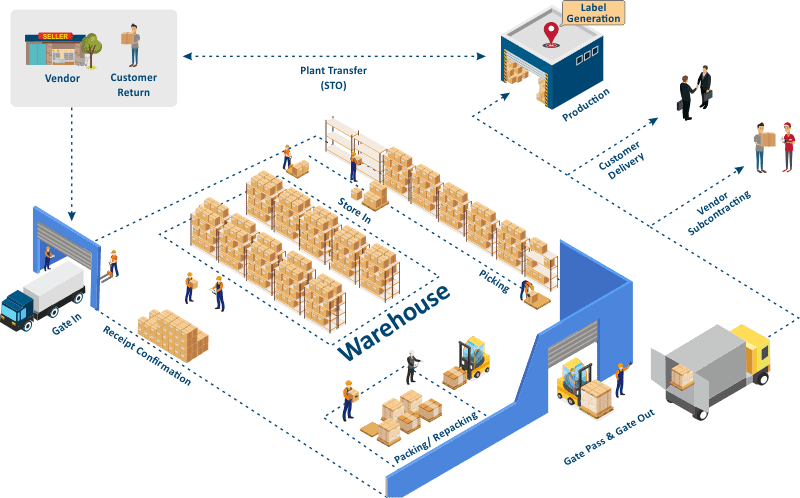
Functional Overview - Scenario
Multiple scenario with flexibility to define moreInbound Movement
- Purchase
- Stock Transfer Receipts
- Production
- Sub-contacting Receipt
- Customer Returns
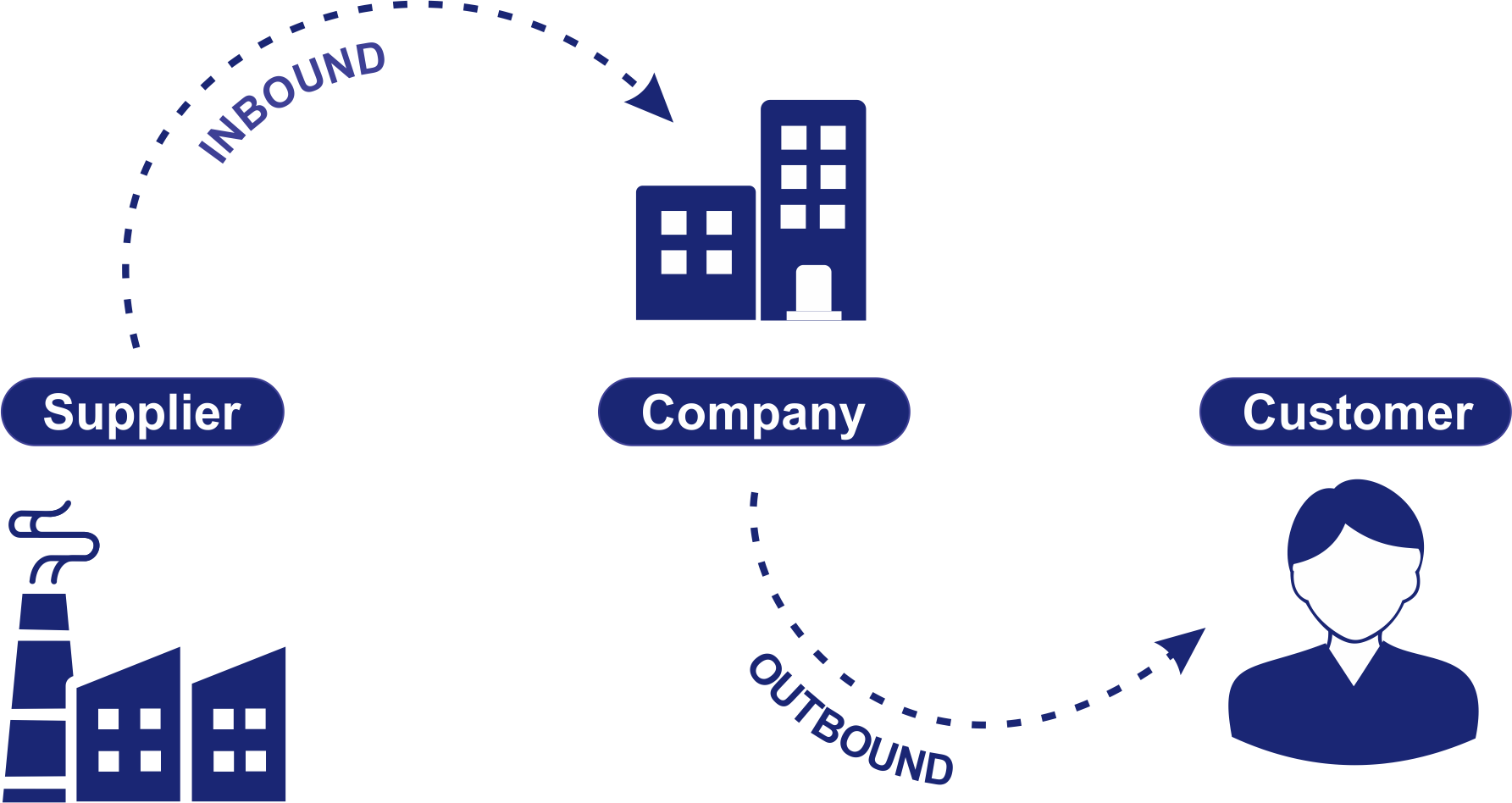
Outbound Movement
- Customer Delivery
- Stock Transfer Issues
- In-house consumption
- Sub-contracting component issues
- Vendor Returns
Functional Overview – Movement
IN BOUND |
---|
Gate-In |
Receipt Confirmation |
Store-In/Put Away |
OUT BOUND |
---|
Picking |
Packing |
Gate Pass |
Gate Out |
INTERNAL MOVEMENT |
---|
Bin Consolidation |
Bin Recociliation |
Special Pick |
Internal Store In |
Special Features
Label Generation
Relabeling
Customer-specific Labelling
Repacking
Batch Management
Quarantine – Batch /
Pack level
Pack level
Controlled Use Stocks
(Semi-quarantine)
(Semi-quarantine)
Multiple pack types
for same product
for same product
Standard Pack sizes
and Odd Lot Packs
and Odd Lot Packs
Loose Parts
Direct-to-Pack
(Cross-Docking)
(Cross-Docking)
Lost and Found
Key Benefits and Enablers
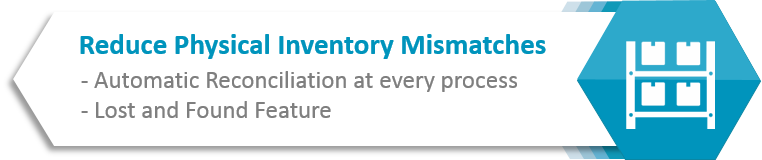
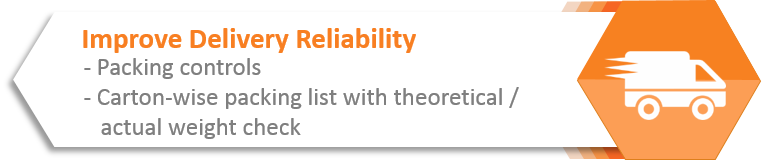
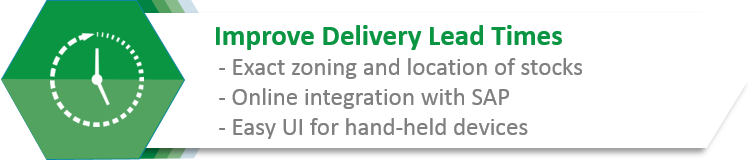
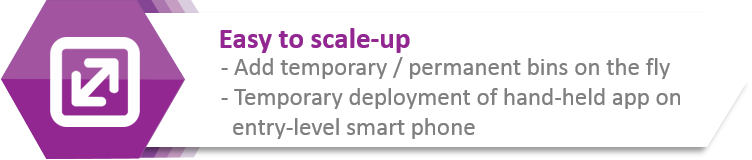
Selected Checks and Balances
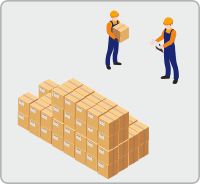
Check: | Valid PO exists with open quantity |
---|---|
System Response: | No confirmation possible against invalid PO |
Benefit: | Eliminates mismatch and Invoice Verification errors |
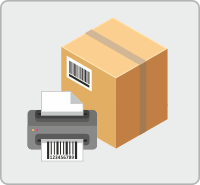
Check: | Material marked as quality-relevant |
System Response: | Label generation not allowed if QC is pending |
Benefit: | Labels printed only for QC approved stock |
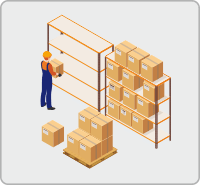
![]() |
![]() |
![]() |
Same material stock exists in warehouse | Store-In proposed in same/ nearby bins | Warehouse consolidation |
Completeness check against plan quantity | Allowed but bin(s) marked for reconciliation | Reduces differences in physical inventory |
Completeness check at bin level | Allowed but bin marked for reconciliation | Reduces differences in physical inventory |
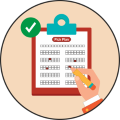
![]() |
![]() |
![]() |
Odd lot stocks availability against odd lot requirement | Odd lot packs are proposed first | Warehouse consolidation |
Combination of same material across pick requests | Combined quantity is planned for a single pick | Higher picking Efficiency |
Available stock at bin level | Bins with least stock are emptied first | Warehouse consolidation |
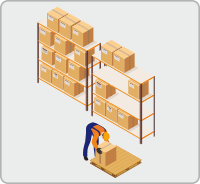
![]() |
![]() |
![]() |
Quality flag of scanned pack | Incorrect quality status cannot be picked | Reduce rework; Improve delivery reliability |
Right material from right location | Incorrect locations marked for reconciliation | Reduces differences in physical inventory |
Completeness check – shortage | Short picked plans cannot start packing | Reduces inventory blockages |
Completeness check - excess | Excess quantity cannot be picked | Reduces clogging at packing stations |
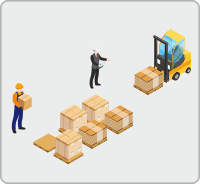
![]() |
![]() |
![]() |
|||
Combination of same ship-to party across pick requests | Different ship-to locations cannot be combined | Improve delivery reliability and efficiency | |||
Material check | Right material, right quality, right quantity | ||||
Customer-specific label requirement | Packing cannot be completed without customer specific labels | ||||
Completeness check - shortage | Cannot be completed if there are shortages | ||||
Completeness check - excesst | Excess packing is not allowed | Reduce leakages | |||
Weight check - shortage | Repacking if actual weight is less than theoretical weight | Improve delivery reliability and efficiency | |||
Weight check - excess | Repacking if actual weight is more than theoretical weight | Reduce leakages |
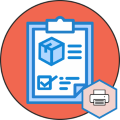
Check: | Packing completeness |
System Response: | Packing list cannot be printed |
Benefit: | Improve delivery reliability and efficiency |
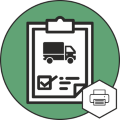
Check: | Packing completeness |
System Response: | Gate pass cannot be printed |
Benefit: | Improve delivery reliability and efficiency |